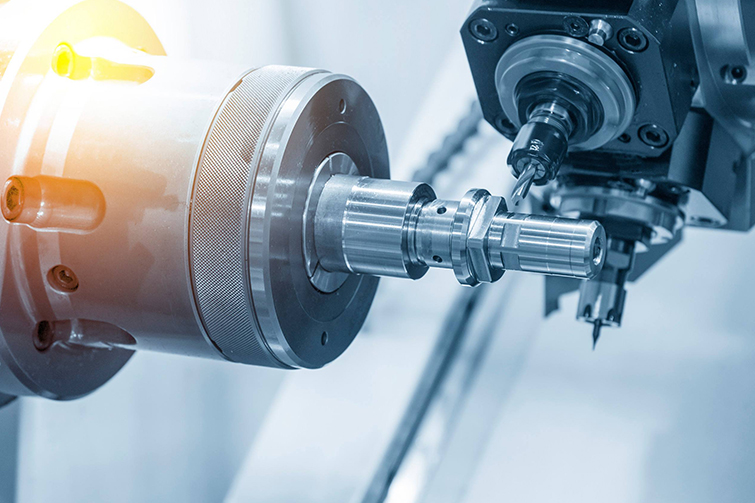

Optimizing Performance with Rotary Cutting Teeth and Auger Drilling Teeth: A Technical Deep Dive
Introduction to Rotary Cutting Teeth and Auger Drilling Teeth
Rotary cutting teeth and auger drilling teeth are critical components in the drilling industry, designed to penetrate and remove material efficiently. These teeth are attached to drilling tools and are subjected to extreme conditions, making their design and material composition vital for performance and longevity.
Design and Material Considerations
The design of rotary cutting teeth and auger drilling teeth focuses on maximizing penetration rates and minimizing wear. Materials such as tungsten carbide are commonly used due to their hardness and resistance to abrasion. The geometry of the teeth, including their shape and angle, is optimized for specific drilling conditions and materials.
Functionality and Application
These teeth are employed in a variety of drilling applications, from mining to construction. Their functionality is influenced by the drilling method, whether it be rotary, percussive, or a combination of both. Understanding the application requirements is crucial for selecting the right type of teeth.
Optimization Strategies
To enhance the performance of rotary cutting teeth and auger drilling teeth, several strategies can be employed. These include regular maintenance, proper alignment, and the use of coatings to reduce wear. Additionally, selecting teeth that match the geological conditions can significantly improve drilling efficiency.
Common Questions
What are the main differences between rotary cutting teeth and auger drilling teeth?Rotary cutting teeth are typically used in rotary drilling applications, designed for cutting through hard materials. Auger drilling teeth, on the other hand, are used in auger drills and are optimized for removing loose material efficiently.
How often should rotary cutting teeth and auger drilling teeth be replaced?The replacement frequency depends on the drilling conditions and material hardness. Regular inspections are recommended to assess wear and determine the optimal replacement time.
Can the same teeth be used for different types of drilling?While some teeth are versatile, it's generally advisable to use teeth specifically designed for the drilling method and material to ensure optimal performance and longevity.