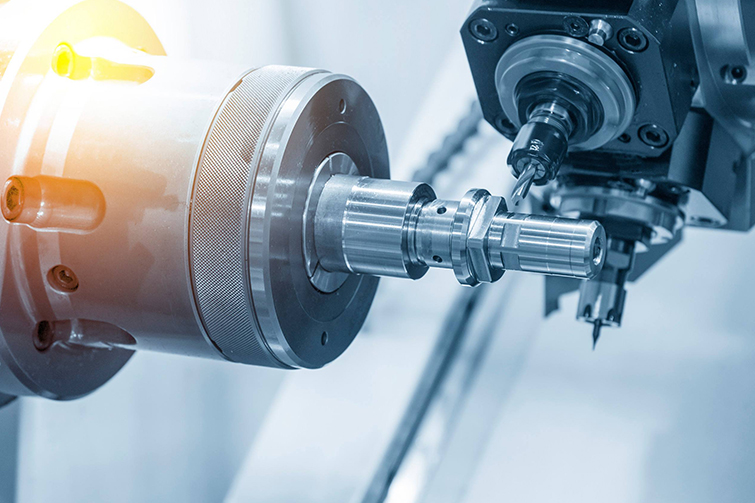

The Comprehensive Guide to PDC Drill Bits: Technology, Applications, and Advancements
Introduction to PDC Drill Bits
PDC drill bits are at the forefront of drilling technology, offering unmatched efficiency and durability in various drilling operations. These bits utilize polycrystalline diamond cutters, which are known for their exceptional hardness and wear resistance, making them ideal for challenging drilling environments.
Technology Behind PDC Bits
The core technology of PDC bits lies in their polycrystalline diamond compact cutters. These cutters are synthesized under high pressure and temperature, bonding diamond particles to a tungsten carbide substrate. This process results in a cutting element that combines the hardness of diamond with the toughness of carbide, enabling the bit to drill through hard and abrasive formations with ease.
Applications of PDC Drill Bits
PDC bits are widely used in the oil and gas industry, geothermal drilling, and mining operations. Their ability to maintain high rates of penetration (ROP) in soft to medium-hard formations makes them a preferred choice for directional drilling and extended reach wells. Additionally, their durability reduces the need for frequent bit changes, significantly lowering operational costs.
Advancements in PDC Bit Technology
Recent advancements in PDC bit technology include the development of 3D modeling and simulation tools for bit design, allowing for optimized cutter placement and hydraulics. Innovations in cutter technology, such as thermally stable diamond layers, have further enhanced the performance and lifespan of PDC bits in high-temperature environments.
Choosing the Right PDC Bit
Selecting the appropriate PDC bit involves considering factors such as formation type, drilling parameters, and bit design. Understanding the specific requirements of your drilling operation is crucial to maximizing the bit's performance and achieving cost-effective drilling.
Common Questions
What makes PDC bits superior to traditional drill bits?PDC bits offer superior durability and efficiency due to their polycrystalline diamond cutters, which can withstand abrasive and hard formations better than traditional materials.
Can PDC bits be used in all types of formations?While PDC bits excel in soft to medium-hard formations, their performance in very hard or fractured formations may be limited. In such cases, hybrid bits or other specialized designs may be more appropriate.
How do advancements in cutter technology impact PDC bit performance?Advancements such as thermally stable diamond layers and improved cutter geometries enhance the bit's resistance to heat and wear, allowing for longer runs and higher ROP in challenging conditions.